Ibuprofen raw material production plants, like some other pharmaceutical plants, generate high concentrations of ammonia and nitrogen wastewater during the production process. The world's largest ibuprofen raw material production plant in China, the plant has a stock of wastewater with ammonia nitrogen content of 3,000 to 5,000 mg/L, the wastewater also contains COD of about 8,000 mg/L, the treatment is difficult. Due to the high organic content in the wastewater, if a blow-off tower or an evaporation tower is used to remove the ammonia, the low volatile organic content will be discharged with the air, resulting in secondary pollution.
Fig. 1: Blow-off tower produces secondary pollution, while the equipment size is large and energy consumption is high.
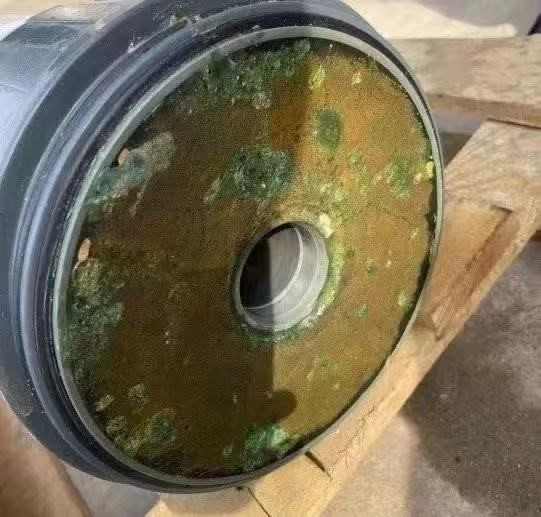
In order to avoid secondary pollution, the plant adopted membrane deamination, but due to the previous technical level, the PP membrane deamination technology pioneered by a U.S. company in the use of the membrane module wetting, low concentration of ammonia sulfate in the absorbent solution and other problems, affecting the effectiveness of the use.
Figure 2: Problems with the PP membrane module
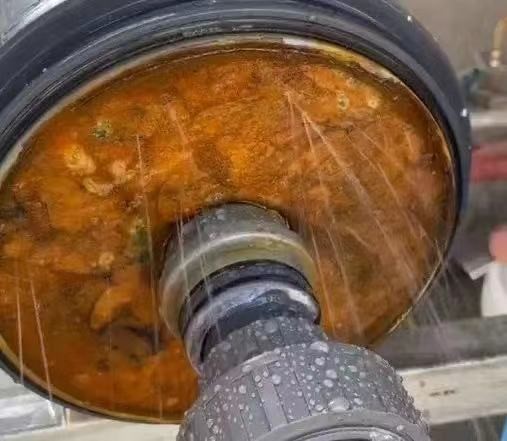
After analyzing and researching, it was found that the problem in the use of its membrane deammonia is the problem of the PP material used in the membrane module. although the PP material has the advantages of low material cost and simple membrane technology, but the PP membrane has a short life span in the use of organic wastewater, and is prone to swelling, wettability, broken filament, etc. The pharmaceutical plant found that the PP membrane has problems in the use of the membrane module, such as low concentration of ammonia sulfate in the absorbent solution. This pharmaceutical plant found that the PP membrane problems, all replaced with Nanjing Zhongke Bidun new membrane PTFE deamidation membrane module, PTFE material, also known as Teflon, that is, non-stick material, itself has the characteristics of anti-dissolution, strong hydrophobic, high-strength, corrosion-resistant, anti-pollution and other characteristics of the long service life, deamination of ammonia and other high efficiency, to overcome the above membrane deamidation in the use of the problem.
Figure 3: More than 40 media reported this unique technology in China.
PTFE material has excellent performance, but the process of making microporous membrane is difficult, researchers from the Chinese Academy of Sciences spent 10 years on research and development for this purpose, and finally commercialized the production in its joint venture plant in Nanjing.
Figure 4: Stable operation after replacing PTFE membrane module
The process of ammonia removal is as follows: adjust PH value of sewage → ultrafiltration → raw water tank → raw water pump → PTFE hollow fiber membrane ammonia removal device (three-stage) → produced water to the biochemical tank. The operation is very stable, and the ammonia nitrogen in the effluent is lower than its design requirements.
PTFE membrane deammonia not only to avoid secondary pollution to achieve pollution reduction and can significantly reduce the consumption of electricity and steam to achieve carbon reduction, while reducing operating costs, in many projects than the use of blowing off or steam ammonia process investment costs are lower. The health and environment of China is improving year by year, not forgetting pollution reduction and carbon reduction.